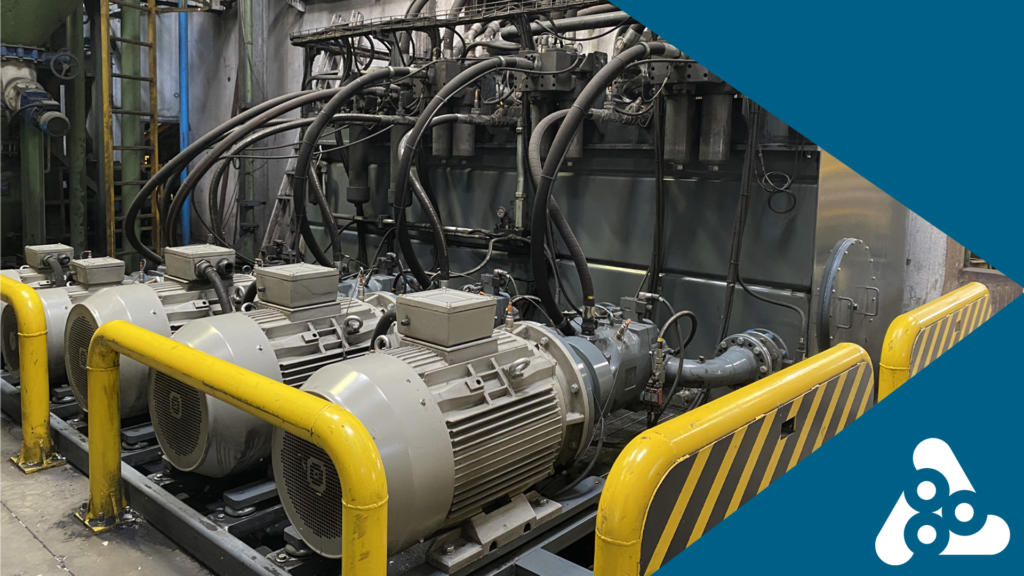
Installation of a new hydraulic power unit for the forming plant with monitoring of the parameters for preventive and predictive maintenance
The project in question was carried out at Fonderia Ghirlandina in Modena in August 2019.
It involved the removal of the two hydraulic power units for the forming machines and for the related movements of the forming plant, and the installation of a single power unit in an area adjacent to the previous ones; the piping and the entire electrical power system also had to be redone.
A single power unit was designed with piston-type main pumps and load sensing pumps for each of the forming machines. The design of this power unit was based on a logic that could ensure at least the same performance as the previous power units, but with a higher overall energy efficiency rating.
The immediate key advantages of this new layout are:
- Environment and safety:
Increased freedom of action for forklift trucks in the forming area
Reduction of noise - Maintenance:
Easy access to the power unit for the purpose of maintenance, resulting in less downtime due to faults
Easy access to belts in the pit for the purpose of maintenance - Logistics:
Storage area for cores near the branching line with a consequent 50% reduction in procurement time
Unification of the hydraulic components in the warehouse - Energy:
Reduction of about 120kW of power during the work cycle of the forming plant, saving an estimated 250,000 kWh of energy per year - Reliability of the plant:
Oil operating temperature between 35 and 50 °C
Uniform line pressure
The latter two factors allow the hydraulic actuators in the forming plant to operate in a smooth and repetitive manner.
The conceptof this hydraulic system is based on the choice of reliable components andsolutions tailored to the actual needs of the plant, while also maintainingsufficient redundancy of the power systems; there are five main motor pumpunits: two of 45kW for the two forming machines and three of 90kW for thepestle and drive circuits.
There are three different cooling circuits, each with its own motor-pump unit and heat exchanger (the latter are already installed on the external wall of the factory), to ensure availability of the system even in the case of a malfunction or maintenance work.
All the circuits are equipped with filters on the de- livery lines, at the outlet ofeach main pump, and on the return lines, directly on the tank, to avoid contamination. The same types of filters are also in- stalled on the coolingcircuit, guaranteeing continuous filtration independent of the work cycles ofthe machines used in the foundry.
Everything has been perfectly integrated into the structure of the main tank with valveblocks and manifolds machined from solid metal in the interest of simple configuration and ease of maintenance.
The filtration system and its sensors are essential to proper operation, reliability and longevity of the system; scientific evidence and practical experience have proven that more than 70% of faults are due to contamination of the hydraulic fluid and wear of the parts.
The hydraulic power unit has therefore also been equipped with a monitoring systemconsisting of software designed by Oleobi and a dedicated portal for managingand viewing all the transducers in- stalled on the sensitive components.
The power unit represents the pilot project of the advanced diagnostics and predictive maintenance system for hydraulic power units developed by Ole- obi and which goes by the name of o-guardian.
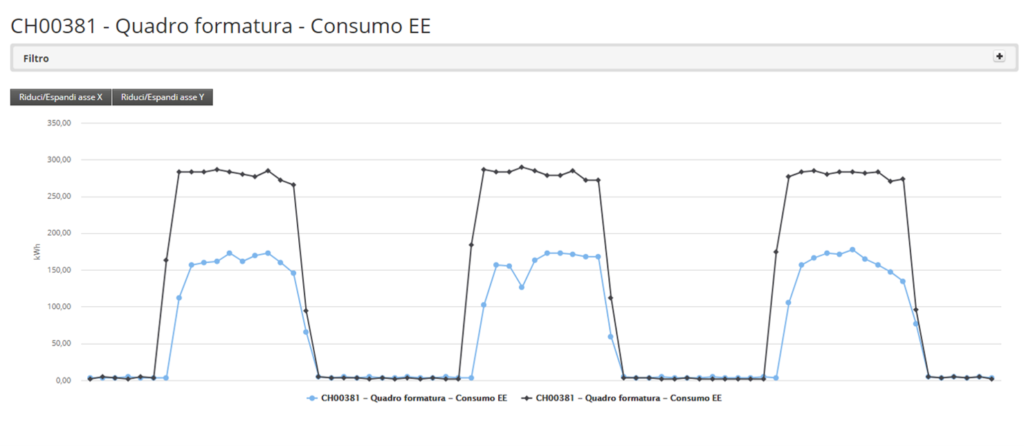
The system allows you to monitor and collect in- formation relating to the hydraulic fluid(level, temperature, contamination, etc.) and to each in- dividual pump (vibrations, drainage, temperature values, etc.)
These datacan be duly interpreted to ascertain the condition of the hydraulic fluid (tocheck for contamination), the state of wear of the pumps (to check the flow of drainage and level of vibrations), the operation of the cooling systems and the performance of the hydraulic systems (to monitor the temperature values).
All theinformation collected is used to send email alerts to the customer who can thentake immediate action in the case of situations that, if not resolved, couldcause the power unit to seize up within a very short period of time (within afew days or hours).
The data from the field are also stored in a cloud- based system for a minimum of 5years and are used to create a predictive diagnostic report on a quarterly basis.
The system offers the following advantages
- Monitoring of all the parameters of the power unit in real time
- Reduction of unexpected downtime with the im- mediate alert system.
- Planning of maintenance with the quarterly predictive diagnostic system