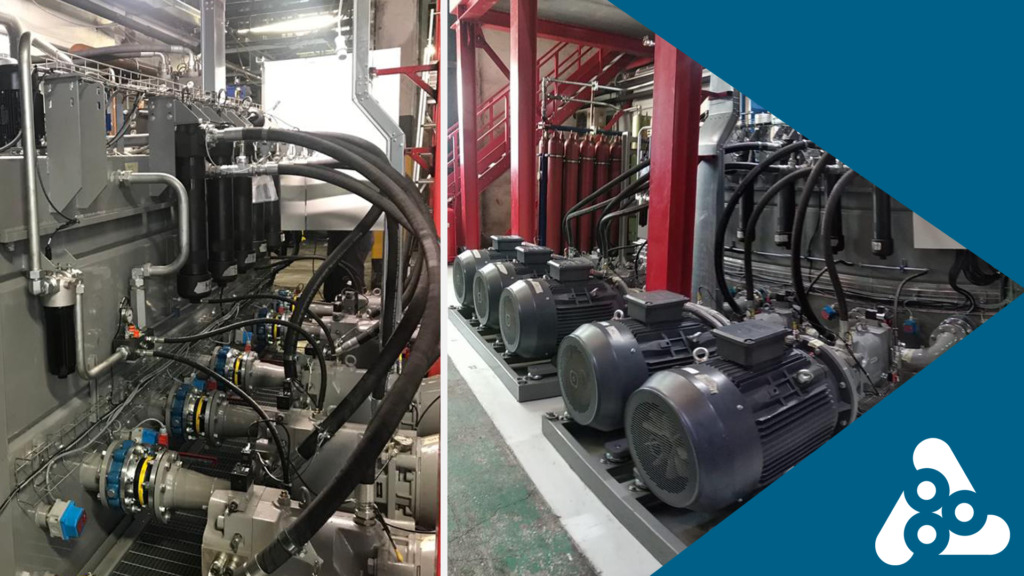
Impianto di formatura più efficiente e fermi produzione azzerati con il nuovo sistema di diagnostica integrato!
La Sfida
In questo particolare scenario economico in cui l’intero globo si trova, diventa sempre più fondamentale cercare di ridurre i costi, aumentare la produttività ed essere prudenti nella scelta degli investimenti. Nel caso di Fonderia Zanardi, la scelta dell’intervento di efficientamento del sistema di formatura è stata più che mirata; la vecchia centrale idraulica non era più in grado di fare fronte ai ritmi ed alla qualità che fonderia Zanardi è solita offrire ai propri clienti.
La soluzione
Oleobi ha studiato a fondo la situazione e le esigenze del cliente che principalmente erano: riduzione dei costi, aumento della produttività, alta qualità del prodotto finale ed è intervenuta realizzando una centrale su misura, più compatta e più performante, modificando completamente la tecnologia dell’impianto idraulico.
La vecchia centrale a 5 pompe è stata eliminata; quest’ultima alimentava in parallelo le due formatrici, le movimentazioni complementari ed i pestelli dell’impianto di formatura.
La nuova centrale, ubicata in una zona adiacente alla precedente, si basa su tre circuiti indipendenti, uno per ogni formatrice e il terzo per i servizi, ciò ha permesso di ottenere una pressione molto più uniforme nelle linee formatrici, ottimizzando la qualità di formatura. Tale spostamento ha comportato in parte il rifacimento delle vecchie tubazioni e di tutta la parte elettrica di potenza.
La centrale è stata progettata con quattro gruppi motopompa in lavoro più uno di scorta che a comando elettrico può sostituire ognuno dei quattro, questa soluzione permette di fare in ogni momento, manutenzione alle pompe senza fermare la produzione; le pompe sono tutte a pistoni a portata variabile con regolatore di potenza costante. La logica con cui è stata progettata questa centrale è quella di ottenere maggiori performances rispetto alla precedente, ma con un’ottimizzazione del consumo energetico globale di funzionamento.
I Risultati
Tale intervento ha permesso il raggiungimento di tutti gli obiettivi prefissati in termini di:
Efficientamento Energetico:
Come evidenziano i seguenti grafici è stato evidenziato un notevole risparmio energetico, stimabile in circa 100 KW/h ,risparmio annuo è valutato in circa 200.000 KW; calcolando un turno lavorativo. Calcolando invece due turni lavorativi come spesso accade nelle fonderie, il risparmio ovviamente diventa del doppio.
Nuova Centrale Vecchia Centrale
Manutenzione:
– accesso facilitato alla centrale per eventuali interventi di manutenzione
Logistica:
– ricavata area in prossimità della linea di formatura per futuro utilizzo (stoccaggio materiali per utilizzo linea)
– unificazione dei componenti oleodinamici in magazzino
Affidabilità impianto:
– temperatura di lavoro dell’olio compresa tra 38-42°C
– pressione delle linee uniforme
La conseguenza di questo ultimo punto, è quella di rendere fluido e uniforme il movimento dei singoli cilindri idraulici operanti nell’impianto di formatura.
Il concetto di questo sistema idraulico si basa sulla scelta di componenti affidabili e soluzioni dimensionate sull’effettiva esigenza dell’impianto migliorando le performance, mantenendo anche una adeguata ridondanza dei sistemi di potenza; infatti i gruppi motopompa principali sono in tutto 4, 2 da75kW per le 2 formatrici e 2 da 75kW per i circuiti dei servizi e traslazioni.
Per quanto concerne il controllo della contaminazione, tutti i circuiti sono stati protetti da filtri opportunamente dimensionati, inserendo filtri in mandata, all’uscita da ogni pompa principale, e filtri sui ritorni montati direttamente sul serbatoio. Inoltre, gli stessi tipi di filtri sono stati installati sul circuito di raffreddamento garantendo una filtrazione continua ed indipendente dai cicli di lavoro delle macchine impiegate in fonderia.
Il tutto è stato integrato al meglio nella struttura del serbatoio principale progettando blocchi valvole e collettori ricavati dal pieno così da garantire un layout semplice e confortevole per la manutenzione.
Sistema di Diagnostica O-guardian
Il sistema di filtrazione e i relativi sensori sono fondamentali nel determinare il buon funzionamento, l’affidabilità e la longevità dell’impianto infatti ci sono evidenze scientifiche e riscontri reali che hanno determinato che più del 70% dei guasti è da imputare a alle condizioni del fluido idraulico in termini contaminazione e grado d’usura. Motivo per cui, la centrale oleodinamica in oggetto è stata dotata di un sistema di monitoraggio in cui tutti i trasduttori installati sui componenti sensibili sono gestiti da un software elaborato da Oleobi e visualizzabili su un portale dedicato.
Il sistema di diagnostica avanzata e manutenzione predittiva per centrali oleodinamiche sviluppato da Oleobi, denominato o-guardian, permette di monitorare e raccogliere le informazioni relative al fluido idraulico (livello, temperatura, contaminazione, ecc.) e di ogni singola pompa (vibrazioni, drenaggio, temperature, ecc.)
Con questi dati, correttamente interpretati si possono
capire in che condizioni si trova il fluido idraulico (controllo
contaminazione), lo stato di usura delle pompe (controllo flusso di drenaggio e
livello di vibrazione) , funzionamento dei sistemi di raffreddamento e
funzionalità dei sistemi idraulici (monitoraggio delle temperature).
Tutte le informazioni raccolte sono utilizzate per generare warning immediati
attraverso un sistema di mailing, permettendo al cliente di intervenire
tempestivamente in situazioni che se trascurate porterebbero al blocco della
centrale in tempi molto brevi e lunghi fermi macchina (ore /giorni).